14. Februar 2007
6. Februar 2007

Jetzt geht es weiter mit dem Fundamentrahmen (gemeinsam für Kessel und Maschine), sowie mit dem Kessel. Propellerwelle (30er, 2 m lang) mit Innendichtung habe ich heute bestellt. Der Laden läuft...!
28. Januar 2007
Irgendwann habe ich es nicht mehr ausgehalten. Ich wollte sehen, wie sich alles dreht und bewegt.
Nach Festlegen der Bedienerseite der Maschine (da wo die Deckel der Schieberkästen sind) und der Stellung der Kulissen für Vorausfahrt, erfolgte die Einstellung des Kolbenschiebers und der Exzenter (zuerst um 90° zur KW versetzt).
Ohne Zylinderdichtungen und ohne Stopfbuchsenpackungen für Kolben- und Schieberstangen. Auch ohne einen richtigen Druckluftanschluss, mit dem Schlauch direkt in die Einlassöffnung eingeschoben. Und auf einen Zylinder... Die Maschine lief auf Anhieb. Herrlich...!! Anschließend habe ich mit der Einstellung der Exzenter und des Schiebers herumgespielt. Alles sehr unempfindlich. Man muss sie brutal verstellen, ehe die Maschine das Drehen verweigert.

Nach dem Probelauf auf einen Zylinder
Die fehlenden Teile für den zweiten Zylinder waren schnell fertig. Dann folgte der Probelauf auf den zweiten Zylinder. Die Kreuzkopfführung war etwas schwergängig, aber ansonstens lief die Maschine wie gewünscht.
Konstruktionsänderungen
In der Zwischenzeit kam es zu einem regen Austausch von Information mit Rainer Radow über die Verwendung von PTFE-Dichtungen für den Arbeitskolben. Die Idee habe ich sofort aufgegriffen und die Konstruktion des Kolbens und dessen Stange in Anlehnung an seine Zeichnungen geändert. Die Idee besteht darin, nur einen Spaltlosen PTFE-Ring einzusetzen, der mit einem Viton-O-Ring unterlegt wird. PTFE und Viton sind Temperaturbeständig bis ca. 200 °C. Die Lebensdauer des PTFE-Ringes sollte stark von der Güte der Zylinderwand abhängen.
Um den Einbau des Ringes zu erleichtern, wird der Alu-Kolben zweiteilig ausgeführt. Eine konische Aufnahme für die Stange und eine geänderte Befestigung am Kreuzkopf kamen auch dazu. Das Material für den Kolben und PTFE für die Ringe wurde schnell gekauft.
Der neue Kolben mit einem PTFE-Dichtungsring
Die Fertigung eines Kolbens mit Stange und PTFE-Dichtung fand übers Wochenende statt. Eine einfache Aufgabe. PTFE lässt sich wunderbar verarbeiten. Es ist sehr dehnbar, so dass der Ring nach dem Zusammenbauen ein deutliches Übermass hatte. Abdrehen im zusammengebauten Zustand auf 66,05 mm. Um Standard-Ringe verwenden zu können, müsste man sich an die richtige Tiefe der Ringnut herantasten, die automatisch die richtige Passung für den Ring ergibt. Obwohl der Kolben bei zu enger Passung nicht klemmt, ist die erforderliche Kraft, um den Kolben zu schieben, groß.
Kolbenunterteil bei der Fertigung
... und der ganze Kolben mit der neuen Stange
Erneuter Probelauf... auf einen Zylinder
Für den erneuten Probelauf konnte ich Zylinderdichtungen und einen vernünftigen Druckluftanschluss mit Regelventil anbieten. Kurz und bündig: herrlicher Lauf, mit nur 0,5 bar.
Der zweite Kolben war ein Kinderspiel (ich hatte ja Erfahrung...). Die Maschine lief auf zwei Zylindern sehr gut, erreichte jedoch nicht die Drehzahl, weil der Druckluftverbrauch einfach größer ist, und der Kompressor nicht mehr lifern kann. Die Maschine lässt sich wunderbar umsteuern, ich brauche nur, die Kulissen anzuticken, da sie von den Exzentern bis zum Anschlag mitgenommen werden.
Jetzt ist Schleifen angesagt. Die meisten Teile haben eine sehr grobe Sandgussstruktur. Anfang Februar könnte ich so weit sein, dass die Maschine in voller Pracht vorgestellt werden kann.
30. Dezember 2006
Die nächste Aufgabe - die Bearbeitung der gabelartigen Pleuelstangen ("fishbone connecting rods") - hat mir große Schwierigkeiten bereitet. Langsam werden die Grenzen der kleinen Werkzeugmaschinen sichtbar, und insbesondere das Fehlen von geeigneten Hilfsmitteln, um die Werkstücke vernünftig zu befestigen.
Die Bearbeitung (alles, was man sich als Amateur wünscht: Einrichten, Vorbohren, Trennen, Gewindeschneiden, Fräsen, Ausdrehen, Reiben) ist deshalb wichtig, weil die kleinsten Abweichungen dazu führen, dass der Kreuzkopf und die ganze Mechanik klemmen.

Das Pleuel im Lieferzustand (Bronze)
Das Teil ist unhandlich, es ist nicht einfach, es an den Bearbeitungspunkten kurz zu befestigen. Mehrere Versuche waren nötig, bis das Rütteln und Schwingen beim Bohren und Fräsen verschwanden.

Versuch 1 mit dem Schraubstock: lange, freie Strecken, große Scwingungen

Versuch 2 mit dem Teilapparat: nicht wesentlich besser

Versuch 3 mit Befestigungswinkel und Pratzen: ja, so ging es...
Das bekannte Problem: große Werkstatt, kleiner Auftrag, wenig Zeit... Kurz vor Weihnachten bekam ich die Teile zurück. Total verbaut, 2 mm aus der Toleranz, es wurde möglicherweise freihändig mit der Bohrmaschine gearbeitet... ich kann es mir sonst nicht erklären. Trost: die "Arbeit" wurde um sonst durchgeführt.

Prüfen der Lagerachsen auf Parallelität: unten 2 mm Abweichung

und mittig wurde auch nicht gebohrt...!
Jetzt ging es darum, die Teile zu retten. Die einzige Möglichkeit war, die Bohrungen von 16 auf 18 mm zu vergrößern, und die Kreuzkopfzapfen mit Buchsen zu versehen. Mit Hilfe einer einfachen Vorrichtung und mit dem Befestigungswinkel war ich doch in der Lage, die Arbeit mit dem Ausdrehkopf sehr genau durchzuführen.

Von hinten durch die Brust ins Auge: Ausdrehen der oberen Lagerbohrungen
Bearbeitung der fehlenden Teile für den Probelauf
Die Stephenson-Kulissen machten große Freude. Nix CNC! Geduldige, stundenlange Einstellarbeit mit Tuschierfarbe und Schaber. Etwas für Rentner... Der Stein gleitet dann spielfrei im Schlitz der Kulisse.

Konusdrehen zwischen den Spitzen: Griff der Stephenson-Kulisse

Gewindeschneiden für die Begrenzungsbolzen
An den Zylindern mussten noch die Bohrungen für Entwässerung (1/8") und Dampfeinlass (1/2")angebracht werden.

Dampfeinlassbohrung 1/2" mit der "automatischen" Gewindeschneidvorrichtung
Die Schwungräder waren bis jetzt nur einseitig gedreht. Meine einzige Möglichkeit, die andere Seite zu drehen, war, das Rad auf eine Stange zwischen den Spitzen zu montieren.
Die Konstruktion des Arbeitskolbens ist sehr einfach, beinahe primitiv (Möglichkeiten einer kleinen Hinterhofwerkstatt Ende des 19. Jahrhunderts). Der Kolben wird direkt auf die Stange aufgeschraubt, eine konzentrische Befestigung ist dadurch nicht möglich, er "eiert". Das Befestigungsgewinde für den Kreuzkopf ist zu lang, führt zum Klemmen. Das alles habe ich nachträglich geändert, mehr dazu später. Für den Probelauf habe ich schnell zwei provisorische Kolbenringe aus PVC gefertigt.

Kreuzkopfführung mit eingeklebten Sinterbuchsen
Jetzt habe ich alle Teile eines Zylinders fertig, die ich für den Probelauf brauche. Im Januar geht es weiter.
26. November 2006
Gießen und Bearbeiten der Weißmetalllager
Die Maschine ist mit drei Weißmetall-Hauptlagern ausgestattet, die allerdings noch gegossen werden müssen. Als die Originalmaschine Ende des 19. Jahrhunderts gebaut wurde, war diese Lagerart Stand der Technik. Die Lager können große Lasten klaglos aufnehmen, haben hervorragende Trockenlaufeigenschaften und sind wirklich anspruchslos. Sie lassen sich leicht einstellen, und können notfalls jederzeit neu gegossen werden.
Das Problem ist, dass die Technik in Vergessenheit geraten ist. Kaum jemand kennt sich heutzutage damit aus. Mit dem Teilesatz bekam ich Weißmetall in ausreichender Menge (eine Zinn/Nickel-Legierung). Die Anleitung des Maschinenherstellers war jedoch mehr als dürftig (Geheimniskrämerei?), die im Internet vorhandene Information ist auch nicht sehr berauschend... Gehirnjogging war also angesagt, auch nicht schlecht...
Ich entschied mich für das getrennte Gießen der oberen und unteren Lagerschalen. Das Prinzip ist an sich einfach: ein Dorn wird oberhalb des Trägermaterials (Lagerdeckel, Grundplatte) so aufgehängt, dass er die Lagerstellen der Kurbelwelle simuliert. Der Zwischenraum wird dann mit Weißmetall ausgegossen. Die Aufhängung des Dorns muss allerdings genau mittig erfolgen, damit später alles zusammenpasst. Entsprechende Ringe sorgen dafür, dass das geschmolzene Weißmetall nicht seitlich ausläuft.
Die Vorrichtung anzufertigen war aufwändig. Diese Arbeit ist aber erforderlich, ohne die Vorrichtung geht es nicht.
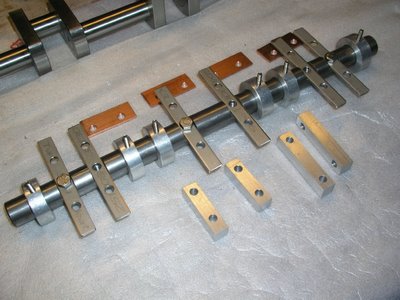
Die Vorrichtung mit Dorn (26 mm Durchmesser), Aufhängelaschen, Abdichtungsringen und Abstandhaltern
Der erste Schritt besteht darin, das Grundmaterial zu verzinnen, um die Verbindung des Weißmetalls mit den bronzenen Lagerteilen zu ermöglichen. Die Aufgabe ist aber nicht einfach, und ohne das richtige Zeug nicht zu bewältigen. Es gibt aber ein Wundermittel: "Paste Castotin 1". Nach Auftragen der Paste mit dem Pinsel wird das Teil von der Rückseite mit dem Propanbrenner auf ca. 280 °C erhitzt. Dabei verbindet sich das Zinn mit dem Bronze, die ausgeschiedene braune Flüssigkeit wird mit einem Tuch entfernt. Die drei Lagerdeckel ließen sich einfach verzinnen, die Grundplatte erforderte wegen der größeren Masse eine Menge Hitze.
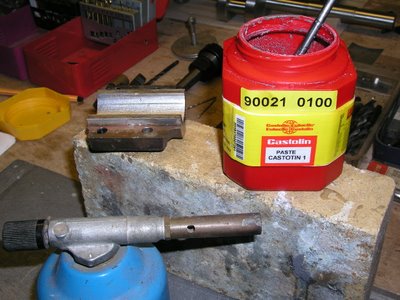
Das "Wundermittel" Castotin 1. Ein Lagerdeckel ist bereits verzinnt.
Ehe man mit dem Gießen anfängt, müssen alle Teile der Vorrichtung, die in direkten Kontakt mit dem Weißmetall kommen, mit einem "Trennmittel" behandelt werden. Mittel, die verbrennen können, sind ungeeignet. Die Lösung: sie werden gerußt, und zwar mit einer sauerstoffarmen Azetylenflamme.
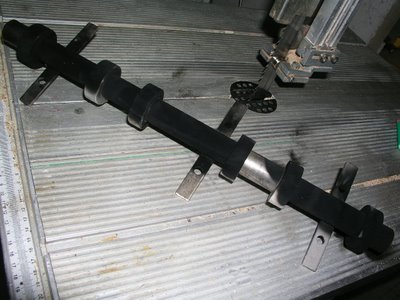
Die mit der Azetylenflamme behandelte Vorrichtung
Ich habe zuerst die drei Lagerdeckel einzeln gegossen. Nachdem sie an der Vorrichtung angebracht waren, mussten sie von unten ordentlich erhitzt werden, damit das Weißmetall nicht sofort erstarrt. Der Dorn musste ebenfalls erhitzt werden. Es ging alles erstaunlich schnell und einfach, mit hervorragendem Ergebnis.
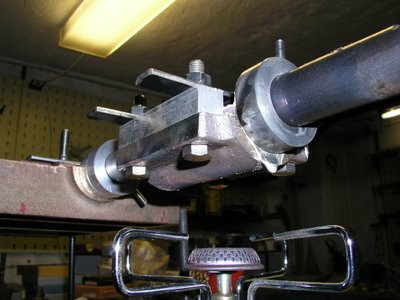
Der mittlere Lagerdeckel nach dem Gießen
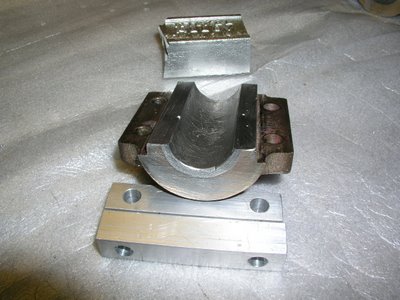
Nach dem Verputzen sieht die Lagerschale ordentlich aus
Die nächste Phase war sehr ernüchtern. Das Gießen der unteren Lagerschalen erfordert eine enorme Hitzeentwicklung, die meine drei kleinen Propangasbrenner nicht liefern konnten. Die äußeren Schalen gingen gerade so, die mittlere (worunter ein Steg der Grundplatte verläuft) war nicht auf die richtige Temperatur zu bringen. Am Ende blieb eine kleine Lücke im Metall, die ich vorläufig als "großzügige Öltasche" betrachte. Später kann ich sie mit anderen Hilfsmitteln neu gießen.
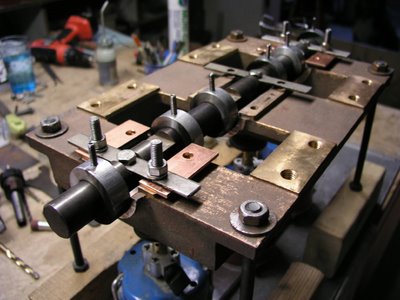
Alles vorbereitet für das Gießen der unteren Lagerschalen
Der Versuch, die erforderliche Hitze zu entwickeln...
Als Nächstes müssen die Lagerschalen abgeschabt werden, um ein gleichmäßiges Tragbild zu erzielen. Alte Technik, die ich von früher kenne. Ein Dreikanthohlschaber war noch in Kiel zu bekommen, Tuschierfarbe aber nicht... Die Spezialwerkstatt, die meine Kurbelwelle zusammengepresst hatte, konnte mir damit aushelfen. Das Tuschieren und Ausschaben der Weißmetallschalen ist eine herrlich entspannende Tätigkeit.
Einer der Lagerdeckel nach Tuschieren mit der blauen Farbe. Daneben der Dreikantschaber. Gleichmäßiges Tragbild
Die Kurbelwelle liegt ordentlich satt auf den Lagern und läuft sehr leicht und spielfrei. Es war eine sehr interessante Arbeit, bei der ich eine Menge gelernt habe. Jetzt weiß ich, wie die Aufgabe das nächste mal zu packen wäre (mit einer andersartigen Vorrichtung, die ich bauen müsste, und einem leistungsfähigerem Brenner).
Endergebnis, Lager spielfrei eingestellt
31. Mai 2006
Abgesehen von gelegentlichen Besuchen in Keller (die Maschine ist noch da...) war ich hauptsächlich als "Schreibtischtäter" aktiv.
Die Pearl-Maschine, die mit einem Kolbenschieber ausgestattet ist, ist für äußere Einströmung vorgesehen. Mir ist diese Auslegung etwas rätselhaft, denn:
1. Der Druck, der auf der Stopfbüchsenpackung lastet, ist höher als bei innerer Einströmung.
2. Bei der vom Hersteller vorgeschlagenen Anschlußstelle für Frischdampfzufuhr (unterhalb des Kolbenschiebers) wird die Einströmung vom Kolbenschieber beinahe abgesperrt, wenn dieser die untere Lage erreicht.
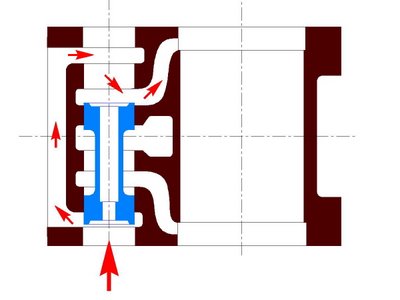
Längsschnitt des Zylinders mit dem vorgesehenen Schieberkolben. Die Kolbenstange befindet sich oben. In seiner unteren Stellung sperrt der Kolben die Dampfeintrittsöffnung ab.
Aus diesen Gründen werde ich die Maschine auf innere Einströmung umstricken. Der Schieberkolben ist dann etwas kürzer und sperrt den Abdampf nicht ab.

Umstellung auf innere Einströmung, Schieberkolben mit Labyrinthdichtung (siehe unten)
Ein Thema, das mich sehr beschäftigt, ist die Zylinderschmierung. Ich weiß, dass bei einigen Konstruktionen ein Mindestmaß an Schmierung nicht zu vermeiden ist, besonders bei Verwendung von Gußeisen oder bei Flachschiebern. Wenn man sich jedoch vor Augen führt, was für ein Aufwand betrieben werden muss, um im Kondensationsbetrieb das Öl aus dem Speisewasser zu trennen, ist die Vorstellung reizvoll, ohne Zylinderschmierung auskommen zu können. Ob es bei meiner Maschine gehen würde?
In dieser Hinsicht kann ich nicht auf die Erfahrung anderer Pearl-Kollegen zurückgreifen. Nicht einmal vom Hersteller ist Information über die Schmierung zu bekommen, geschweige die Adressen von anderen Kunden. In Frankreich werden zur Zeit zwei Einzylindermaschinen gebaut, beide jedoch in der Gußeisenausführung. Es sieht so aus, als lediglich zwei Zwillingsmaschinen in Europa verkauft wurden. Die andere (hallo Hans) wird z.Zt. in Schweden zusammengebaut, ist aber auch ein Gußeisensatz.
Bei meiner Maschine sind Zylinder und Kolbenschieber aus Bronze. Wegen der Ringkanäle muss der Schieberkolben ohne Ringe auskommen. Die Abdichtung wird deshalb durch eine sehr enge Passung erreicht. Die Materialpaarung (Bronze/Bronze) scheint zuerst ungünstig zu sein. Da es jedoch keine Reibung stattfinden sollte, ist die Paarung hinsichtlich der Wärmedehnung ideal: die Passung bleibt bei verschiedenen Temperaturen konstant.
Nun zur Zylinderschmierung. Die Maschine wird mit Sattdampf betrieben. Würde eine Art Labyrinthdichtung am Schieberkolben (schmale, 1-mm-Nuten, wie oben dargestellt) ausreichen, um eine ölfreie, schwimmende Lagerung zu erhalten? Der Aufwand für Versuche ist nicht groß, so ein kleiner Kolben wird schnell gedreht.
Es bleibt jetz der Arbeitskolben. Im Gespräch mit dem Eigentümer des DB "Felizitas" erfuhr ich, dass sie mit Kunststoff-Kolbenringen (Werkstoff unbekannt...) experimentieren, die jedoch nicht lange halten. Titan wurde auch genannt (??), das jedoch einen viel geringeren Wärmeausdehnungskoeffizient als Bronze hat.
Wie wäre es mit dem Motto: probieren geht über studieren? Ich würde mich sehr über Vorschläge und Anregungen freuen.