Beschreibung der Pearl-Maschine
Ich hatte anfangs die Gussteile für die Einzylindermaschine gekauft, da mir ihre Leistung für das vorgesehene Boot ausreichend schien. Erst später bestellte ich die fehlenden Teile, um die Zwillingsmaschine zu bauen. Sie besteht praktisch aus zwei Einzelmaschinen, die auf einer großeren Grundplatte festgeschraubt sind.

Einzylindermaschine in der Bronzeausführung
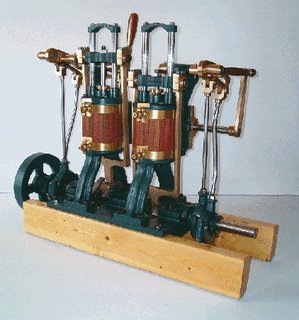
Zwillingsmaschine in der Bronze/Gusseisen-Ausführung
Die Einzylindermaschine ist der maßstabgetreue Nachbau der 1880 von Edward S. Clark in Massachussetts gebauten Dampfmaschine, die für den Antrieb von privaten Dampfbooten eingesetzt wurde. Die Maschine - mit einer Bohrung von 2,5" und einem Hub von 3" - ist deshalb außergewöhnlich, dass die Kolben- und die Kolbenschieberstangen nach oben zeigen. Dadurch sind die Stopfbuchsen direkt von oben zugänglich, was die Wartung erheblich erleichtert. Da konstruktionsbedingt die Pleuelstangen länger sind, verbessert sich der mechanische Wirkungsgrad der Maschine.
Die Maschine wird von Pearl Engine Co. in Sutton, Vermont, in verschiedenen Fertigungsstufen angeboten: Gusssätze (Bronze und Gusseisen), vorbearbeitete Sätze und fertige Maschinen. Die Zwillingsmaschine ist eine eigene Entwicklung von Pearl Engine Co., Edward S. Clark hatte damals nur die Einzylindermaschine gebaut.
Sie ist wirklich spartanisch und einfach gehalten. Die zusammengesetzte Kurbelwelle (später mehr dazu) ist auf Weissmetalllagern gelagert. Pearl hat eine Einhebelmechanik für die Stephenson-Umsteuerung entwickelt, die ich nicht einsetzen werde (gefällt mir nicht...).
Meine erste Aufgabe bestand darin, die mitgelieferten Zeichnungen (Zoll-Abmessungen) mit Autosketch neu zu zeichnen. Soweit das Material es zuließ, habe ich mich für runde mm-Abmessungen entschieden. Ebenso habe ich die Bohrung auf 66 mm (statt 2,5 Zoll = 63,5 mm) und den Hub auf 80 mm (statt 3 Zoll = 76,2 mm) vergrößert.
Die Zwillingsmaschine hat ein "Indicated Power" von 4 PS, ohne weitere Angaben... Sie ist eine der Maschinen, die für den Antrieb des Elliot-Bay-Rumpfes vorgesehen sind, jedoch im unteren Leistungsbereich.
Mein "Maschinenpark"
Für die Metallverarbeitung verwende ich - seit vielen Jahren - zwei kleine, aber präzise Werkzeugmaschinen von EMCO: die Drehbank Compact 8 und die Fräse FB-2. Sie erlauben mir, alle Teile der Dampfmaschine zu bearbeiten, mit Ausnahme der Zylinderbohrungen für Kolben und Kolbenschieber. Nachteil ist, dass sie nur mit manuellem Vorschub ausgerüstet sind. Geduld ist bei einigen Arbeiten angesagt...
Ich habe nachträglich die Drehmaschine mit einem Schnellwechsel-Stahlhalter und einer Digitalanzeige ausgerüstet. Gebrauchte Stirnwalzenfräser, Scheibenfräser, Reibahlen (alles bei eBay erstanden) haben sich gut bewährt.
Durchgeführte Arbeiten
Es gibt keine zwingende Reihenfolge der Bearbeitung. Um langsam "auf Betriebstemperatur" zu kommen, habe ich mit leichten Aufgaben angefangen. Bronze-Gussteile sind angenehmer zu bearbeiten als Gusseisen, die erfordern jedoch viel Aufmerksamkeit.
Die Bearbeitung der Grundplatte war tricky. Die Bewegung des Koordinatentisches reichte nicht aus, um alle zu fräsenden Flächen in einem Aufspann zu erreichen.
Grundplatte
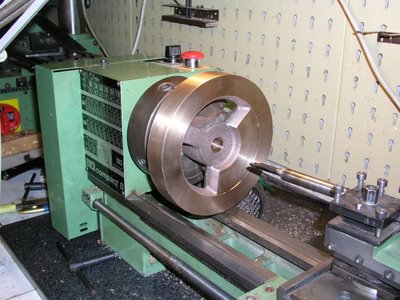
Schwungrad
Die vier Exzenter und ihre Bügel waren reine Freude
Der Zylinderdeckel mit der Stopfbüchse und die Lagerung für die Führungsbolzen stellte keine großen Schwierigkeiten, genauso wie die Verbindungsbrücke für die Führungsbolzen.
Zylindeerdeckel mit Führungsbolzen
Problematischer waren die beiden Schlitten. Vorgesehen war der Einsatz von Sinterhülsen als Gleitfläche. Da meine Kreuzkopfschlitten aus Bronze sind, verzichte ich auf sie.
Schlitten
Die beiden Böcke (pedestals) mit der Zylinderaufnahme waren unhandlich (beinahe zu hoch für die kleine Fräse) aber unproblematisch.
Die Halterungen für die Kolbenschieberbetätitung waren anspruchvoll, genauso wie die einzelnen Teile und Hebel für die Schieberbetätigung.
Halterung
Unteres Gelenk für die Schieberbetätigung
Um die Stephenson-Kulissen zu bearbeiten musste ich mir eine Vorrichtung ausdenken (einfach und primitiv...), die gut funktioniert hat. Der letzte Schliff fehlt noch.
Stephenson-Kulisse
Bearbeitung der Zylinderbohrungen
Die Bearbeitung der Zylinderbohrungen habe ich bei einem Betrieb durchführen lassen, wo ein ehemaliger Flugkamerad tätig ist. Die Kolbenbohrung wurde ausgespindelt, die Schieberbohrung vorgebohrt und gerieben. Alles natürlich mit einer riesigen CNC-Maschine, wobei die Programmierung einen halben Tag dauerte... Das Ergebnis ist phantastisch, und der Preis hielt sich in Grenzen.
Bearbeitung mit der NC-Maschine
Wieder im Keller: Bohren und Gewindeschneiden für die Halterung der Schieberbetätigung
Fertigung der Kurbelwelle
Kommen wir nun zur Kurbelwelle. Nach den Originalzeichnungen ist die Kurbelwelle aus einzelnen Teilen zusammengesetzt, die nach Ausrichten mit Kegelstiften gesichert werden. Bin aber ein gebranntes Kind und halte wenig von zusammengesetzten Kurbelwellen. Die kleinste Verdrehung der Kurbelwangen am Kurbelbolzen führt dazu, dass die Welle schlägt (häufig bei Flugmotoren nach einer Bruchlandung...). Ich beschloss, die Kurbeln (Wangen und Bolzen) aus einem Stück (VA-Stahl) zu fertigen. Und das mit meiner kleinen Drehmaschine! Pro Kurbel war ich ein ganzer Tag beschäftigt. Die Fertigung der Wellenteile war problemlos.
Ich hatte vorher das Thema bei einem Betrieb in Kiel besprochen, der Kurbelwellen zusammenpresst und schleift. Keine Schrumpfung, sondern reine Gewalt: mit 60 Tonnen werden die Teile zusammengesetzt. Dafür musste ich aber für die richtige Passung sorgen, 5 Hunderstel Übermass müssten sein, nicht mehr und nicht weniger.
Ein geliehener Innenmikrometer zeigte, dass die Bohrungen für die Wellenzapfen - obwohl in einem Aufspann abgedreht - ihre eigene Persönlichkeit entwickelt hatten, mit Unterschieden von +/- 1 Hunderstel. Entsprechend mussten die Zapfen auf Mass gebracht werden, was volle Konzentration und viel Geduld erforderte.
Nach dem Zusammenpressen lief die Welle absolut rund. Danach wurde sie geschliffen. Ein schönes Stück geworden, wie ich finde.
Detailaufnahme einer Kurbel
... und das Ganze
Es ist noch allerhand zu tun, darunter wichtige Sachen, wie z.B. das Giessen der Weissmetalllager. Aber die Maschine nimmt Formen an.
Alle Teile lose zusammenmontiert
Momentan sind das Boot und der Kessel dran. Aktualisierungen folgen sobald ich weitermachen kann.